Best Welder For Automotive
Article by Mark Trotta
My old 1970 Chevelle had rust spots on the bottom of the fenders and quarter panels, and behind the quarter panels inside the wheel wells. After stripping the paint down to bare metal, I cut out the rust spots, fabricated patch panels, and MIG-welded them in.

That was 20 years ago. Since then, I've welded countless patch panels and completed dozens of assorted welding projects. All were done with a portable 110-volt MIG welder.
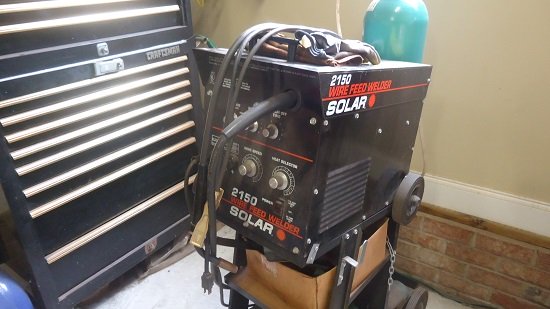
The Solar 2150 MIG machine had been doing a good job with sheet metal and steel up to 3/16", but always struggled with anything thicker. And then after nearly 20 years of part-time use, it stopped working (fan comes on, no spark).
Parts and service for a Solar welder are nowhere to be found. I called two local repair places. One said, "We don't work on those", the other said "We can't get parts for them."
Seems that Solar was bought out by Century Manufacturing sometime in the nineties, then Century was acquired by Lincoln Electric in 2003. Which leads me here, searching for a suitable replacement.
**************************
Types of Welders
To help select the best welder for automotive sheet metal repair and restoration, I've written out an overview of the different types of welding processes. Some are easier to get started with than others, some are less expensive than others, and some take more time to master.
The most common types of welders are Gas, Stick, TIG, and MIG.
Gas Welding - Pros and Cons
Gas welding is the oldest form of welding. Having an Oxy-Acetylene set-up in your home garage allows you to heat up stubborn bolts and pre-heat parts. Having a rosebud tip allows you to cut through thick metal. However, it's hard to learn and difficult to weld thin metal.
Stick Welding - Pros and Cons
Stick, or Arc welding, is easy to learn, doesn't require a gas bottle, but does require a lot of clean-up. It's great for all kinds of garage projects, but not a good choice for thin sheet metal.
TIG Welding - Pros and Cons
TIG welding is neat and precise, but the most difficult to learn. It is also the most expensive welder to buy.
Of the four processes, the most versatile for all-around automotive use is the MIG welder. With a good quality machine, the home hobbyist and classic car enthusiast can repair automotive sheet metal as well as fabricate brackets, repair exhaust systems, make special tools, etc.
Advantages of MIG Welding
- Easiest welding process to learn
- Produces cleaner welds than Stick welding
- Provides good control on thinner metals
- Can weld steel, stainless steel, and aluminum
- Good for out-of-position welding
Disadvantages of MIG Welding
- Difficult to use outdoors
- Paint and rust need to be cleaned off thoroughly before welding
- Very smoky and throws sparks
The MIG Welding Process
A MIG welding machine uses a spool of wire fed through a hand-held gun. Squeezing the trigger controls the wire output. Because of this action, starts and stops are easy, which makes it quicker to learn than Stick or TIG. The arc is created by an electrical current between the base metal and the MIG wire, melting the wire and fusing it with the metal.

MIG welding is faster and more economical than other processes, and well suited for thin metal. Although set-up time can be time-consuming, the actual MIG welding process is relatively quick.
**************************
Wire-Feed vs MIG Welding
Two types of welding can be done with a Mig welder - Mig and flux-core. In other words, you can weld with shielding gas or without shielding gas.
Most inexpensive wire-feed welders run on standard 110v current and are very portable. These small, gasless welders sell for as little as $150, but they are very limited as to what they can actually weld.
Both the Mig and flux-core techniques are relatively easy to learn and give clean welds on steel, aluminum and stainless. Both have the capability to weld materials as thin as 26-gauge.
**************************
MIG Weld With Flux Core
The two major limitations of Mig welding is that it can be difficult to use outdoors (wind can blow away your shielding gas), and that you have to cart around a gas bottle. Flux-core welding, also known as wire-feed welding, does not require gas, instead using a flux-cored wire to shield the arc.
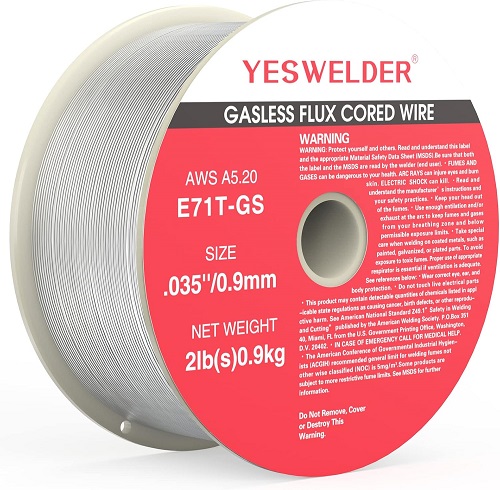
Gasless Flux Core Mig Wire is effective when you need to weld outdoors, in windy conditions, or on dirty materials. However, flux-core is not the best choice for thin sheet metal.
**************************
MIG Weld With Shielding Gas
As it's name implies, the metal inert gas (MIG) welding process uses a shielding gas to "shield" the molten puddle from the atmosphere. The shielding gas is fed through the gun, and basically "suffocates" the weld area from oxygen.
Argon/CO2 Shielding Gas
The most common shielding gas for MIG is an Argon/CO2 mix, which will provide clean, good looking welds on thin sheet metal. If you're an Amazon shopper, you can have a MIG welding tank delivered right to your door.
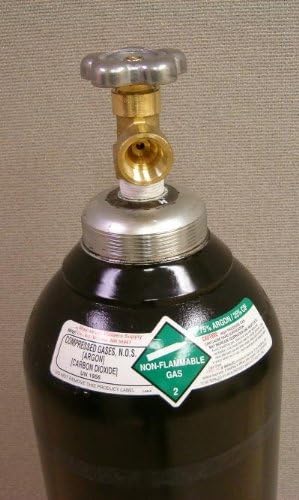
Note: Because of it's contents, delivery requires a signature.
**************************
Duty Cycle
Many inexpensive MIG welders that run on 110-volts will have a high current, but only for a short time. This duration is called the duty cycle, and the higher it is, the more welding you can do in a particular time.
**************************
110v vs 220v Welder
When MIG welding sheet metal, a short, one-inch bead is laid down, then a pause in time, while the welder moves to another point to weld. This procedure is designed to avoid warpage. So a smaller, 110v unit is usually adequate for the hobbyist looking to weld automotive sheet metal.
220-volt welders will feature a higher current with longer duty cycles. These large Mig units can provide up to 250 amps with a 60% duty cycle. These are capable of welding up to 3/8" steel in a single pass, but units like these generally retail for $2,000 and up.
**************************
Best Brand Mig Welder
There are many brands of welders, the better-known American companies being Miller, Lincoln, Hobart, and Forney. Not all components are American made, and most are assembled in the U.S. from foreign and U.S. sourced components. The important thing to remember is that these brands are serviceable.
U.S. Brands vs Chinese Brands
Presently, and for some time, the welder market has been flooded with Chinese-made units. These include Everlast, Longevity, Harbor Freight, Eastwood, and others. Many of these welding machines are the same unit, sold under different brands.
Think about five or ten years from now, if your welder stops working, where can it be fixed? Will you be able to get parts? The advantage here goes to U.S. brand welders, who are established and have service centers in every major city.
**************************
Forney Easy Weld
With a 140 amp max output, the Forney Easy Mig gives you a lot for your dollar. In addition to welding sheet metal as thin as 24 gauge, it can also weld 3/16 to 1/2" metal. High and low settings are variable, and the duty cycle is 30% at 90 amps.
Included with the purchase is a two-pound spool of 030" wire, MIG gun, ground clamp, and 20A-15A adapter. Standard Tweco 1 style consumables will fit the torch. The Forney Easy Weld is assembled in the USA.
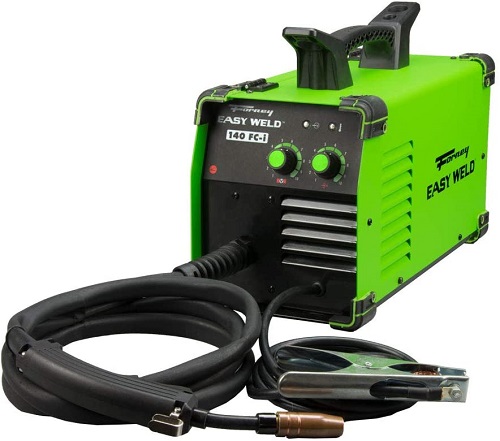
Shop: Forney Easy Weld
Forney provides their customers real customer service. Many of their reviews include stories of first-timers reaching out to the company, speaking with actual live techs on the phone to help diagnose their problem.
**************************
Hobart Handler 140
A few steps up from the Lincoln Handy MIG is the Hobart Handler 140. It also runs off 110v standard household current, and has an amperage output of 25 to 140. Duty cycle is 20% at 90 amps.

Shop: Hobart Handler 140 MIG Welder
Included with the Hobart Handler 140 is a built-in gas valve, 10 foot MIG gun with liner, dual-gauge regulator and gas hose, ground cable and clamp, extra .030 contact tips, and a spool of .030 flux-cored wire. The Handler 140 is Hobart's most popular MIG welder, and welds automotive sheet metal with ease.
**************************
What Size MIG Welder Is Best?
Buying the cheapest unit available is false economy. The expression, "You can't weld with amps you didn't buy" is true.
Consider that a larger machine will retain more resale value if you ever decide to sell or trade. If you think that someday you may want to weld anything thicker than 3/16", you'll want a welder that goes up to (or past) 120 amps. Preferably about 130 amps or above with a 30 amp minimum setting. These will go low enough for bodywork but will have enough power to do occasional thicker stuff.
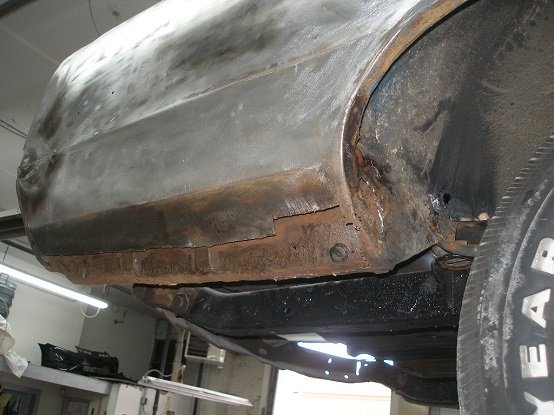
Best MIG Welder For Automotive Restoration
Personally, I have found the best MIG welder for automotive sheet metal is a 110v unit that has 30-140 amps. If it's in the budget, look for one with at least a 20% duty cycle at 140 amps. Medium-sized Mig units like these retail between $450 to $750.
**************************
While you're budgeting for a MIG welder, be sure to include gloves and a welding helmet.

**************************
There are many ways to hold metal in place during the welding process. These magnetic V-pads offered by Stronghand Tools are relatively small and work best with 1/4"to 3/8" thick metals.
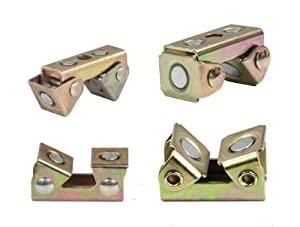
Shop: Magnetic V-Pads
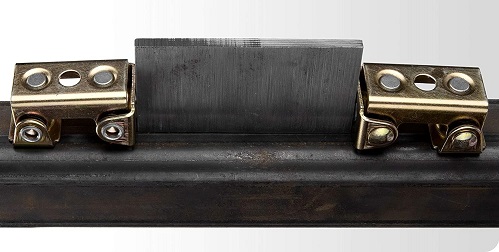
**************************
Related Articles:
How To MIG Weld Sheet Metal
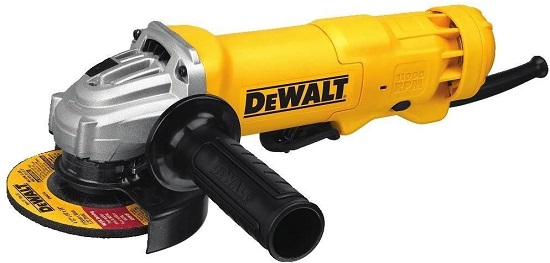